Project Name: Innovative processing technologies for biobased foamed thermoplastic
Open Call Topic(s): Green transition in Europe
Description
VITAL will develop innovative thermoplastic processing solutions for foamed thermoplastics, based on three b-bTP processing value chains: 3D printing process based on granulated feedstocks; Bead foaming process and a Foam Injection Moulding (FIM) process. For foamed thermoplastic processing value chains to make the transition to sustainable, circular economy based on bio-based solutions it is imperative that the critical limitations are overcome. VITAL is an important step on this journey as it will (for the first time) create innovative high efficient, low-cost processing solutions and key enabling knowledge to achieve commercially viable “Sustainable by Design “approaches based on b-bTPs. Adoption of the VITAL outputs across the polymer processing sector, along with the vocational training programme, will therefore make it easier for manufacturers to adopt b-bTPs commercially, achieving a paradigm shift towards bio-based alternatives for cleaner, more climate-neutral industrial value chains. VITAL will stimulate the uptake of sustainable-by-design advanced materials and processes, not just by overcoming technical limitations but by achieving “buy-in” from processors, OEMs and customers, all of whom are represented in the consortium.
VITAL’s objective is to develop innovative processing solutions for foamed b-bTPs, based on three processing value chains chosen based on some commercial-scale processing requirements.
- FIM -
The FIM process consists of a granulated thermoplastic that is blended with a blowing agent, which expands the material, and this blend is injected into a mould. For this kind of process, significant work has been undertaken on the use of supercritical fluid. Otherwise, biopolymers processing variables and characterisation information are still scarce, reducing the implementation of b-bTPs in this value chain.
To address the scarcity of b-TPs information, VITAL will create a unique database of foamed b-bTPs properties that will be critical for future commercial exploitation, while also developing a FIM processing approach based on a Digital Twin with virtual AI control to handle the final characteristics of foam produced.
- Bead foaming of b-bTPs -
Bead foaming produces small beads that can be moulded into complex parts by welding the beads, usually with steam. This method is used for polypropylene and polystyrene. However, b-bTPs show problems with the use of steam due to hydrolysis-sensibility that causes degradation.
VITAL aims to create a bead foaming process for b-bTPs based on radio frequency. The development of radio frequency moulding technology will increase the use of b-bTPs into the bead foaming process because it removes steam and reduces hydrolysis while reducing energy usage.
- 3D b-bTPs foam printing -
3D printing is the construction of a three-dimensional object from a digital 3D model without needing a pre-existing mould. Those objects could be made of steel or polymers, and there is a different process of 3D printing. The Fused deposition modelling uses filaments of thermoplastic material and is the most common 3D printing process in 2022.
The production of 3D foam printing using b-TPs as raw materials are not developed, so VITAL aims to have achieved a globally unique 3D printing process which uses granulate feedstock and produce foams of different densities.
Reason for applying to HSbooster.eu services
The project needs help in 1) Determining relevant standards information (biopolymers and recycling materials) for the design and optimisation of materials and/or processes and requirements for target applications; 2) Existing and applicable standards; 3) Reviewing and advice on the impact of results on existing standards and how to add to / or influence standardisation changes; and, 4) Support with road mapping VITAL project results for into supporting the existing and/or upcoming bio-based material standards.
Main standardisation interest
Considers standards when looking at new materials, product design and manufacturing. Closely related to recyclability and circularity by design to influence standards for recycling and reusing b-bTPs.
Project Acronym: VITAL
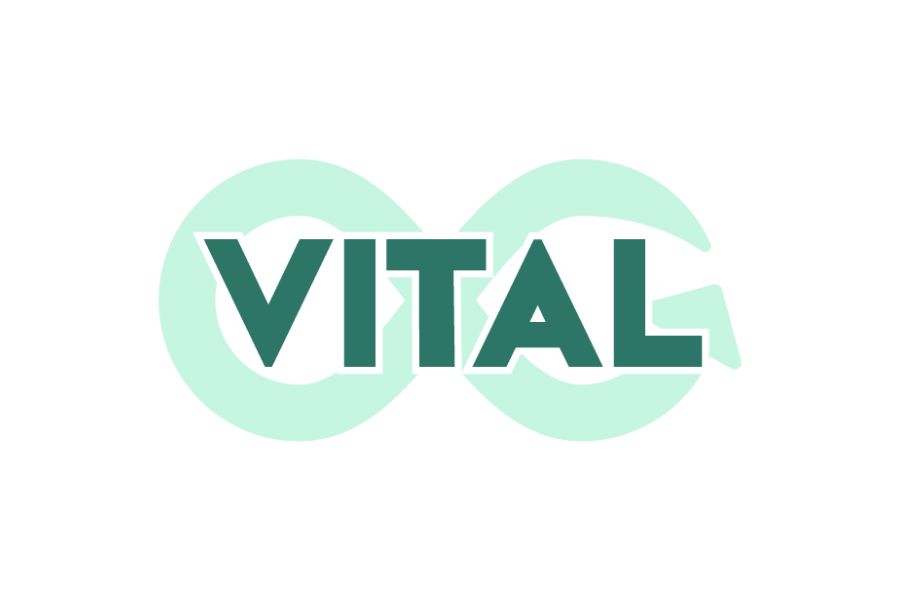
Grant Agreement Id: 101058328
Start Date:
End Date:
Programme: HorizonEurope
Call for proposal: HORIZON-CL4-2021-TWIN-TRANSITION-01-05
Funding Scheme: HORIZON-RIA