Project Name: Sustainable manufacturing and optimized materials and interfaces for lithium metal batteries with digital quality control
Description
The SOLiD project will create a sustainable and cost-efficient pilot scale manufacturing process for a high energy density, safe and easily recyclable solid-state Li-metal battery. It will use roll-to-roll (R2R) dry extrusion coating for the blend of cathode active material, solid polymer electrolyte, and conducting additives. R2R slot die coated primers on the cathode current collector will enhance adhesion, performance and corrosion resistance of the cell. The polymer electrolyte layer will be R2R coated, using an optimal design for the slot die head. For the Li metal anode, it will utilise cost-efficient R2R pulsed laser deposition, which enables minimising the Li thickness down to 5 µm. The Li metal production will be combined with an inline process for interfacial engineering to ensure compatibility with the other layers and stability. The process development will be supported by digitalisation methods to go towards zero-defect and cost efficient manufacturing. The proposed methods enable sustainable manufacturing of Gen. 4b solid state batteries with minimised amount of critical raw materials (Co and Li), and with superior performance and safety: The protective layers enable the use of NMC811, which reduces the amount of Co into minimum without compromising the lifetime, and PLD process helps to minimise the Li thickness. Dry coating eliminates the use of toxic solvents and energy-consuming drying steps, and the digital quality control will reduce the amount of waste. The thickness of each layer will be minimised to reach energy density above 900 Wh/l. Cost will be reduced by cost-effective production methods and by maximising the yield. Safety and long cycle life are guaranteed by the solid electrolyte and the protective interlayers. Supported by the life-cycle thinking and stakeholder engagement, the SOLiD project will enable the design for a sustainable solid state battery factory of the future.
Reason for applying to HSbooster.eu services
They would like to know the standardisation landscape relevant to their project and also any potential gaps in the existing standards.
Since many processes in the SOLiD project are initiated through materials synthesis and electrode manufacturing stage, such as the layering of the Cu substrate, Li-metal anode coating, protective layer coating on Li, SSPE/BSPE synthesis & manufacturing, laser cutting process, and even there is still no 100% applied standard for the solid-state battery cell assembly & activating cycle assessment (they can adopt liquid state, but still there is some different and need adjustment), therefore, they would prefer the standardisation mapping can be done for the whole process.
Project Acronym: SOLiD
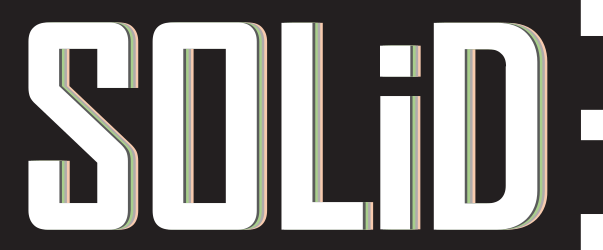
Grant Agreement Id: 101069505
Start Date:
End Date:
Programme: HorizonEurope
Call for proposal: HORIZON-CL5-2021-D2-01-05
Funding Scheme: HORIZON-RIA